BCP’s composite panels are manufactured by bonding aluminium honeycomb core in between two skins. The outer skins are most commonly made of materials such as aluminium, wood, formica and laminates but a wide variety of surfaces can be applied.
Aluminium honeycomb core is highly desirable due to its incredibly high strength to weight ratio. The core used in BCP’s composite panels is manufactured by our sister company, Corex Honeycomb from our Cambridgeshire, UK headquarters. Made with Aluminium Alloy Grade 3003 or 5052, it follows a complex manufacturing process as outlined below:
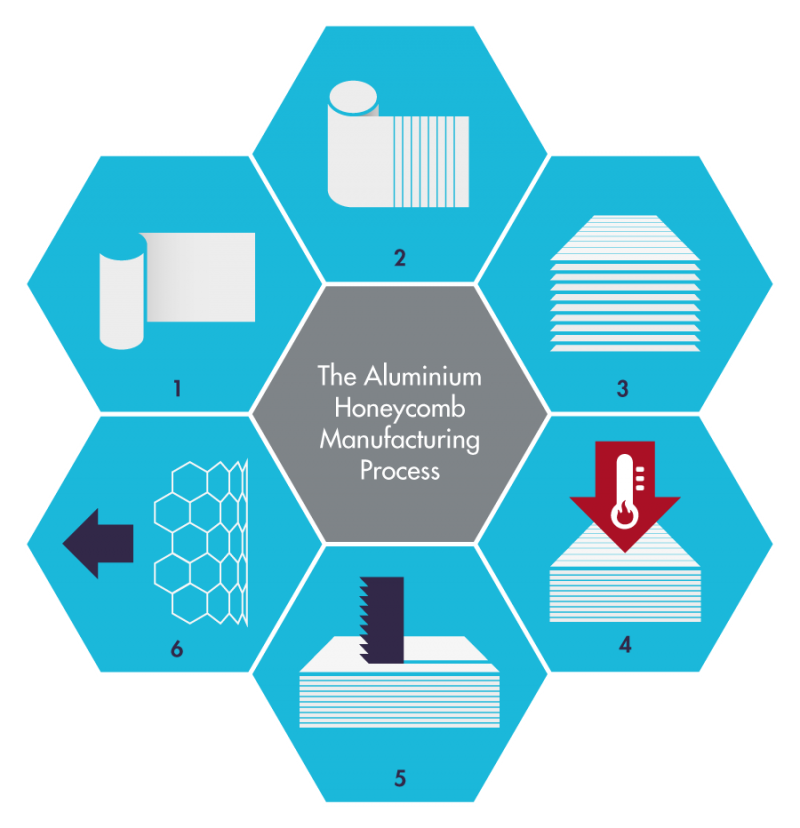
- The manufacturing process begins with a roll of aluminium foil.
- The aluminium foil is passed through a printer for adhesive lines to be printed.
- It is then cut to size and stacked into piles using a stacking machine.
- The stacked sheets are pressed using a heated press to allow the adhesive to cure and bond the sheets of foil together to form a block of honeycomb.
- The block can be cut into slices. The thickness can be custom-made to customer requirements.
- The honeycomb is then expanded.
Finally, the expanded aluminium honeycomb core is bonded together with the customers specified skins to create our bespoke composite panels.
These panels deliver rigidity and flatness with minimal increase in weight and help our customer’s to save on cost, weight and materials.
Honeycomb Cell Sizes
Corex Honeycomb’s core is available in a wide variety of cell sizes:
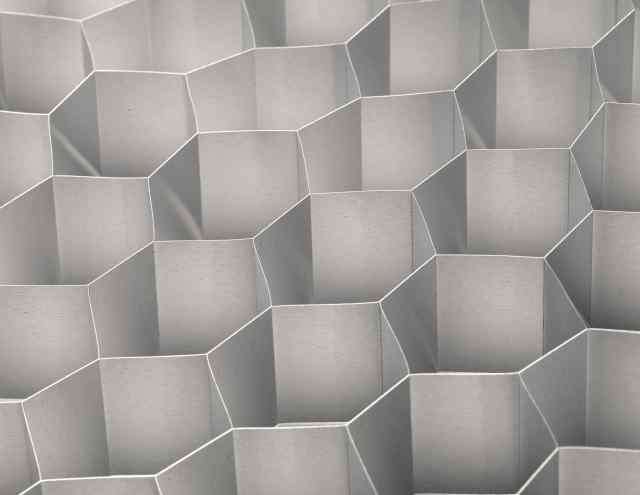
Large Cell Size
Size 25.4mm/ 1”, 19.1mm/ 3/4”
Light and cost effective. Suitable for less demanding applications such as large panels used in architecture, interior design and building facades.

Medium Cell Size
12.7mm/ 1/2”, 9.5mm/ 3/8”, 6.4mm/ 1/4”
Very good strength, weight and cost ratio. Suitable for a range of applications including marine, rail, construction and motorsport.
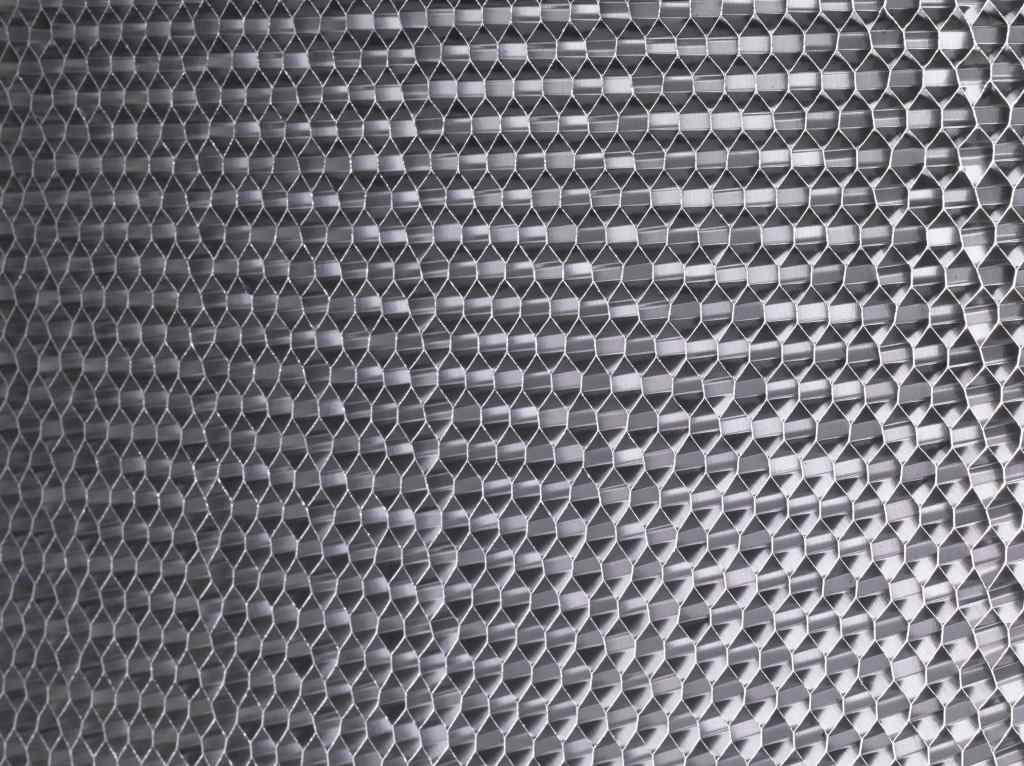
Small Cell Size
4.8mm/ 3/16”, 3.2mm/ 1/8”, 1.6mm/ 1/16”
Higher density honeycomb, making the material heavier than larger cell sizes but achieving the highest strength available. Most commonly used to create extremely resilient sandwich panels.
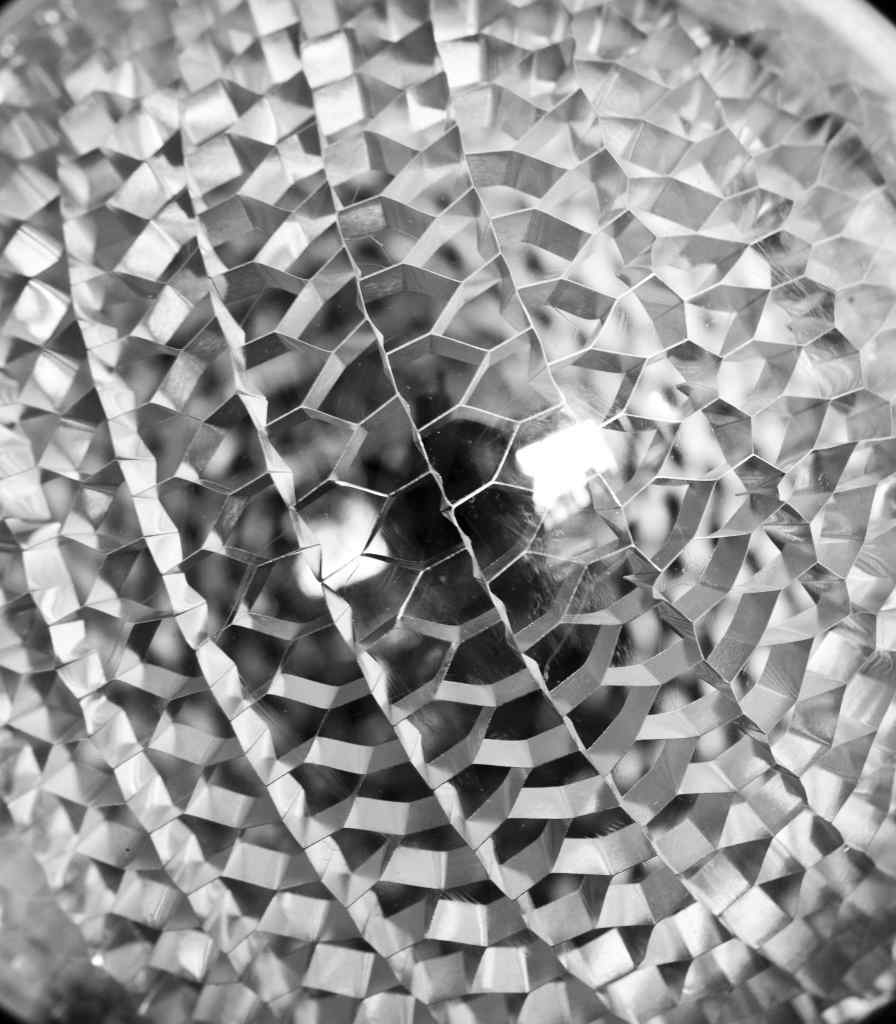
Corex Honeycomb also manufactures SuperFlex, a flexible aluminium honeycomb which has the same properties as standard aluminium honeycomb, but its cell geometry has been adapted so the aluminium honeycomb can bend and flex.
Flexible honeycomb retains its cell shape and strength, making it ideal for BCP’s curved panels used in applications including train interiors, architectural structures, boat hulls, car and caravan body panels.
To find out more about the aluminium honeycomb used to manufacture BCP’s composite panels visit Corex Honeycomb.